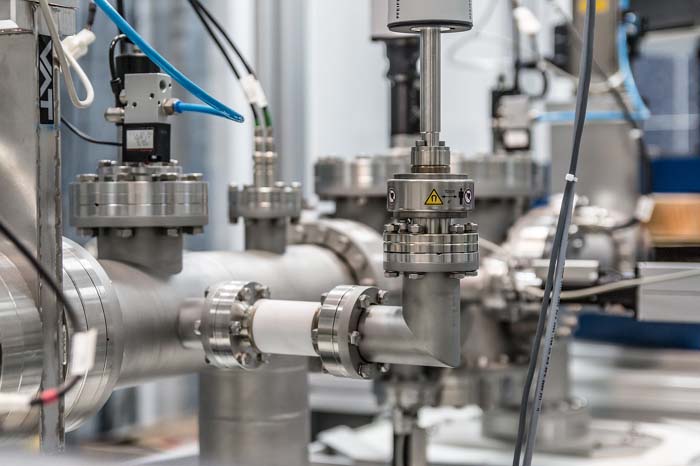
Cleaning the process plant by hand is a labor-intensive and dangerous task. It may take a lot of time, money, and effort and may not get the job done well. Automated Clean-in-place systems mechanically clean the entire process plant, including all pipe circuits, tanks, and fittings, to eliminate residues. Without opening or taking apart the equipment, the Clean-in-place system automates this operation. The goal of creating this cleaning technique was to make it fast, effective, and reliable.
The primary objective of these systems is to rinse water through chemical (disinfectant and detergent) solutions. This will help to clean product contact surfaces to a certain standard. With the system in place, operators are protected from potentially dangerous chemicals and from having to enter restricted spaces.
What Is Membrane Clean-in-place?
A CIP technique is one way to keep the inside of RO membranes clean. Cleaning the water treatment system is possible using membrane Clean-in-place without disassembling it. Clean-in-place uses a cleaning solution to clean and rinse. During routine operations, foulants build up on membrane surfaces; this process removes them.
If you want your reverse osmosis system to work properly and safely, you must perform membrane Clean-in-place. For optimal results, using the correct cleansers to eliminate foulants and precisely adhere to the cleaning instructions is essential.
The Steps of Membrane Clean-In-Place?
A 7-step Clean-in-place process includes things like,
- Pre-Rinse
- Caustic Wash
- Acid Wash
- Intermediate Wash
- Final Wash
- Sanitizing Rinse
- Air Blow
Nevertheless, only some processing lines respond to the same set of instructions. While all Clean-in-place process steps are standard, the specific order in which they work differs from one processing line to the next.
The Steps of the Clean-in-place System are as follows:
Pre-Rinse
As part of the Clean-in-place process phases, internal tank surfaces, fittings, and flushing the lines are strategic steps. The main goal is to get rid of most of the remaining residue. This includes partially melted fats and dissolved carbohydrates.
There is no chemical pressure test for the Clean-in-place flow channel. RO water, deionized water, or potable plant water are excellent choices. Another option is to reuse the water used for the last rinse after the Clean-in-place stage.
Caustic Wash
The caustic wash will soften the fats for easier removal. You can restore the caustic wash multiple times by returning it to its tank. Energy, chemicals, and water can all be significantly reduced by doing this.
Intermediate Wash
Any traces of caustic wash detergent are removed throughout this cycle of wipes. Level probes and transmitters keep an eye on the wash and rinse tank levels.
Flow transmitters make accurate control of the washing and rinsing processes possible. On the other hand, the chemical levels stay within the specified range of the conductivity transmitters.
Final Wash
A last rinse with potable, RO, or deionized water eliminates any remaining chemical residue or material. In the following cleaning cycle, you can save money by recovering and reusing the water from the last rinse as a pre-rinse solution.
Sanitizing Rinse
As the last stage in the Clean-in-place process, this helps destroy pathogens and microbes. Before starting the next production batch, it checks if the food is safe and clean.
These additional Clean-in-place process steps are available as options in the system and can be used as needed during the cleaning process:
- Use an air blower to evaporate any excess moisture.
- Acid Wash (To Reverse the Caustic Wash’s Alkaline Effect)
- Push out the water (the step before pre-rinse that improves cleaning and increases product recovery).
It is possible to automate and optimize many Clean-in-place systems. This makes them a viable and efficient option for preserving cleanliness and hygiene in a variety of industries without causing pipe breakdowns.
How often is CIP done?
There are numerous benefits to Clean-in-place technology for the liquid processing industry. However, many older systems are very resource-intensive. They also waste a lot of cleaning chemicals, electricity, and water. However, this system can still cause substantial downtime, even if it usually doesn’t require extensive disassembly and cleaning.
Production stops for the duration of the Clean-in-place procedure. Typically, it takes about 60 to 90 minutes for one CIP cycle. When the process is repeated several times a day, the costs for manufacturers can add up quickly.
The 4 principles of CIP?
Time
The Clean-in-place process culminates with time as its last pillar. Even a well-designed system will produce subpar results without sufficient time to run.
In contrast to other factors, time is usually objectively determined in the field by tracking the time required to attain the Clean-in-place objective. Before going on to the next phase, each Clean-in-place or rinse solution should be run through the entire circuit at least 5 times to guarantee thorough cleaning.
- Mechanical Action
Just letting components come into contact with a hot Clean-in-place solution is seldom adequate to remove most soils, even after a good soak. The only surefire way to physically remove dirt from surfaces is to use mechanical action, such as scrubbing. Cascades in vessels and turbulent flow in pipes are common manifestations.
For regions that aren’t water-logged during cleanup, such as vessels, impingement, which involves striking areas with water jets, is another option. Here is where spray balls and other specially designed spray gadgets come in handy for cleaning those inaccessible places.
The measurement of mechanical action occurs indirectly. This is done by keeping an eye on flow rates calibrated to generate the appropriate velocity for the specified pipe length and size.
- Chemical Concentration
The usual method for monitoring chemical concentration involves using conductivity sensors and timed doses. For Clean-in-place systems, the chemical is mixed in a closed loop. This allows the solution to reach and stay at a certain concentration before the cycle timers for washing the system start.
Conductivity is also important to guarantee chemical removal before the rinse phase finishes its cycle. Even when heated to almost boiling, some substances nevertheless refuse to dissolve. For this reason, in developing these systems, it is essential to use appropriate chemical selection.
Most soils or organic compounds can be broken down by combining caustic solutions with water and then rinsing with water. After the caustic cycle, the surface is acid-washed and rinsed with water to remove any remaining stains, minerals, or inorganic substances. Following the acid and caustic cycles are the sanitation cycles.
Sanitation cycles using hot water usually range from 180 to 200 degrees Fahrenheit. Another option is to use a chemical sanitizer, which can work at room temperature. However, a chemical sanitizer is another chemical that requires more resources (money) to acquire, store, and oversee.
- Temperature
To make sure heat gets to the whole system, the Clean-in-place circuit return header records and monitors temperatures.
These systems’ typical operating temperature range is 140 degrees F. to 170 degrees F. As a result, the source header’s temperature increases as it exits the Clean-in-place. When planning a system, it’s important to keep temperature in mind.
A greater temperature is produced by increasing the heat input to a system. Better solubility and, by extension, cleaning capability are associated with higher temperatures.
While this may hold water in certain applied disciplines, additional problems crop up when a system gets close to its critical point. Increased operator risk can arise at pump intakes. This is due to cavitation caused by boiling, which is essentially uncontrolled.
Pressure causes boiling to occur. Water, when heated to 212 degrees Fahrenheit in an open pot at atmospheric pressure, will, as is widely known, boil into steam. On the other hand, up to a temperature of 312 degrees Fahrenheit, water at 80psi maintains its liquid state.
Your plumbing system will experience a hammer if the circuit pressure drops and this water turns into steam. Another reason pipes don’t last as long as they should is that carbonic forms during the unintended phase between shifts of condensate and steam. This acid damages the pipe wall.
There is more entropy, enthalpy, and internal energy in a system at higher temperatures. Atmospheric pressure allows the liquid to escape if the transport pipe system develops a leak or hole.
In a moment, the water transforms into superheated steam with higher energy. This poses a threat to nearby people, structures, and machinery. Steam has a higher internal energy than water; hence, steam injuries are more severe at a given temperature than water injuries.
The cost and inherent risk of the Clean-in-place process increase. This is because there’s a need to achieve and sustain higher temperatures.
The advantages and disadvantages of the CIP system?
Advantages
Industries that need to clean and maintain their pipelines and equipment on a regular basis might greatly benefit from these systems. Among the many advantages of these systems are:
- Compliance with Rules:
Industries, including biotechnology, pharmaceuticals, and food and beverage, have specific cleanliness and hygiene regulations that these systems should meet.
- Consistent Cleaning:
To guarantee that pipelines and equipment are always cleaned thoroughly, Clean-in-place systems can provide a consistent and repeatable cleaning procedure.
- Decreased Downtime
With Clean-in-place systems, there’s no need to disassemble the equipment when cleaning. This keeps production schedules intact and decreases downtime.
- Enhanced Safety:
Clean-in-place systems can lessen the likelihood of accidents and injuries sustained by construction workers. This is done by reducing the amount of time spent cleaning by hand.
- Maximized Effectiveness:
These systems automate the cleaning process, allowing for faster and more efficient cleaning of equipment and pipelines compared to traditional techniques.
Disadvantages
There has to be room in the production area for a Clean-in-place installation. Additionally, it has to be customized to fit the production process. Because of this, it is important to take stock of the manufacturing process and meticulously plan the cleaning stages and quality standards. A specific amount of capital is needed for this. However, it will not hinder the cleanup procedure in any way. It makes it better.
What industries use Clean-in-place systems?
Many different types of businesses use cleaning-in-place systems. This is because they know that hygienic conditions are important to the quality and safety of their products. The following sectors frequently employ these systems:
- Research Laboratories
These systems are effectively clean research laboratory equipment like filtering systems, chromatography columns, and reaction vessels. This eliminates the possibility of cross-contamination, shortens the time between trials, and guarantees accurate and reliable findings.
- Pharmaceuticals and Biotechnology:
The biotechnology and pharmaceutical industries rely on these systems to clean the pipe systems and equipment that produce biologics and drugs.
- Brewery:
Brewing and distilling equipment, including that used to make wine, spirits, and beer, can benefit from Clean-in-place systems.
- Dairy:
Equipment used to make cheese, milk, and other dairy products can be cleaned using these systems in the dairy industry.
- Food and Beverage:
The systems are extensively popular in the food and beverage sector. This is to clean all pipes and equipment that come into contact with food items.
The overall goal of Clean-in-place systems is to preserve product quality across all industries by preventing contamination, keeping food at a consistently high standard, meeting hygiene laws, and preventing the growth of bacteria.
Conclusion
Efficient cleaning solutions are essential in the processing, food, pharmaceutical, and beverage industries. Supporting clean processing procedures that adhere to stringent industry standards is made efficient with cleaning in place.
Processing equipment can be rapidly and wholly cleaned using clean-in-place systems without disassembling. Higher output, reduced downtime, and improved product safety are just a few advantages enjoyed by businesses that implement Clean-in-place solutions.