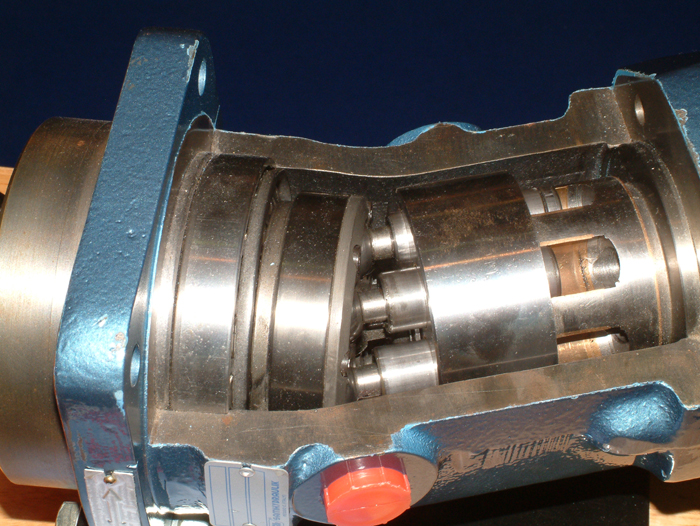
One type of positive displacement pump is the piston pump, while another is the plunger pump. These pumps use a cylinder chamber and a reciprocating piston or plunger to transfer media. Because of their ability to handle mediums, which are both viscous and solids, these pumps go by various names, including high-viscosity pumps, high-pressure pumps, and well-service pumps.
What is a piston pump?
Another component of piston pumps is a rod known as a piston. This moves in a reciprocating motion to push liquid through a series of valves. In contrast to plunger pumps, the seal of a piston pump is integral to the piston. It allows it to rotate in synchronization with the piston within the cylinder.
To what extent are piston pumps efficient?
With an efficiency ranging from 85 to 90 percent, a piston pump is among the most efficient pumps currently available. These pumps do not require a gearbox because they can operate directly from motors or via guarded V belts. This is typically a factor contributing to the losses in the transmission.
What are piston pumps used for?
Examples of typical uses for plunger and piston pumps include applications requiring a low flow rate of a liquid at high pressure, such as chemical injection into pressurized pipework or filtration of seawater for reverse osmosis.
For metering and batching applications, a piston pump is predictable. This is because of its positive displacement design, which means that the volume dispensed is proportional to speed.
These types of designs can only work with pure liquids. They should not have any abrasive or solid particles that could shorten the lifespan of the units, destroy the seals, or cause internal components not to seal and clog.
Such designs can manage to handle saltwater, chemicals, and fuels, but they aren’t always the best choice for situations that call for a self-priming pump. They typically necessitate a flooded suction or, in the case of high-flow units, a booster pump.
Some of the most popular applications include:
- Coating feed for spray bars used to apply polymers, fats, and other coatings to items
- Hydroblasting and hydro-excavation
- Boiler tube or heat exchanger descaling.
- Transfer of fuel
- Drill-cutting injection
- Using pressure washers for a variety of plant equipment cleaning and washing needs, including pallets, bottles, conveyors, kegs, and more
- Using reverse osmosis to purify salt water into drinkable water.
- Pressure testing of equipment and hydrostatic
- Removing concrete from pipes or rebar, cleaning the hull, and removing rust, labels, graffiti, and paint are all part of the surface treatment.
- Maintain clean and abrasion-free seals on other pumps by sealing the flush feed pump.
- Misting to eliminate smells, fogging to control nozzles, and fluid misting using nozzles
- Chemical injection
What is a plunger pump?
The reciprocating plunger, which is a rod, makes plunger pumps work. It takes liquid in through an inlet valve and pushes it out through an outlet valve as it oscillates. The cylinder housing of a plunger pump is fastened to a stationary high-pressure seal.
The advantages and disadvantages of a plunger pump?
One type of reciprocating pump is the plunger pump, which uses a cylinder to force fluids or gases through a chamber. Many industries rely on them for high-pressure pumping and precision control, including chemical, oil and gas, and hydraulic systems. Here, we’ll go over some of a plunger pump’s uses, benefits, and drawbacks.
Advantages
- Low maintenance:
They are also low-maintenance due to their straightforward design. Plunger pumps are less likely to break since there are fewer moving parts.
- Versatility:
These devices are adaptable and can process a variety of fluids, including those with high viscosity or corrosive properties.
- Accurate control
Using plunger pumps, You can regulate fluid flow rate with pinpoint accuracy. They can measure and dose fluids at a precise flow rate.
- High-pressure pumping:
A plunger pump is ideal for a wide range of uses that call for the generation of high-pressure fluid flows.
Disadvantages
- Possibility of leakages
Contamination and fluid loss can occur if the pumps develop leaks.
- Inadequate flow rate
When compared to other pump types, plunger pumps’ flow rates are quite modest. Their primary use is in situations that call for low-flow, high-pressure pumping.
- Noise:
Using a plunger pump at high rates could cause it to make a lot of noise.
- Expensive:
There are more affordable pump options available than plunger pumps. Applications requiring high-pressure pumping and precise control over the flow rate often use them.
The difference between a positive displacement pump and a plunger pump
Positive displacement pump
Pumps that use positive displacement technology mechanically transport the fluid through a system by repeatedly closing off a fixed volume. Simply put, a positive displacement pump moves fluid by using the change in volume within the pump cylinder. Vanes, rollers, screws, diaphragms, gears, and pistons can all power the pumping motion, which is cyclical.
Centrifugal and positive displacement pumps are the two most common types. Higher flow rates and the ability to operate with liquids of lower viscosity are two advantages of centrifugal pumps. A staggering 90 percent of pumps in certain chemical plants are centrifugal. However, positive displacement pumps are the way to go in a lot of situations. For instance, they work better at high pressures with modest flow rates. They can also manage fluids with a higher viscosity. When precision in dosing is paramount, they outperform the competition.
Among the several types of reciprocating pumps utilized, plunger pumps are by far the most prevalent. They maintain a constant flow rate of fluids pumped by them despite variations in the pressure at the pump’s outlet.
The number-one cause of plunger failure
Unfortunately, plunger pumps do break down from time to time. For this reason, there’s no pressing need to rush out and get a replacement pump. If the failure is due to a common plunger pump problem, hire a professional to rectify the issue. These issues usually include the following:
- Oil leakage
Inspect that the breather cap isn’t loose, the bolts on the diaphragm head are snug, and the oil cap is on. Additionally, make sure there isn’t too much oil in the pump.
- The pump motor won’t turn on
A lot of things could cause this to occur. Open thermal overload, blown fuse, motor damage, limit switch or timer open circuit, or low line current are among the causes.
- Reduced pump capacity
Verify the same problems as before. Further reasons could include the liquid’s proximity to its boiling point, insufficient or excessive suction lift, an excessively high viscosity of the fluid, or an improper capacity setting.
- The pump operates unsteadily
Always place a strainer in the suction line to prevent debris from entering a pump during installation. This will ensure that the piping is clear in the event of a blockage. Be sure the pipe’s diameter is greater than or equal to the suction connection.
- Motor overheating
There can be issues with the temperature outside, the wiring, the hydraulic oil’s viscosity, or the voltage. It is important to verify that the motor controlling the pump discharge has a pressure rating.
- Very noisy pump
Some potential causes include worn bearings, too much gear wear, and insufficient lubrication.
- Issues with auxiliary equipment
All auxiliary equipment must be appropriately sized, including the pipes and pump. Controls, calibration cylinders, pulsation dampeners, safety relief valves, and back pressure are all part of this.
- Improper placement of the pump
Because the pump’s efficiency is sensitive to temperature variations, its placement in your building can be problematic.
- Unreliable old seals
When it comes to seals, operators and engineers often need more faith in older systems’ reliability and durability. Before starting operations, this needs checking.
- The pump is operating, but it does not deliver
It may be due to an improperly installed valve if the pump is not operating even though the motor is turning. Look for other issues, such as an unprimed pump, filthy or damaged valves, a clogged suction or discharge line, or a lack of hydraulic oil.
Conclusion
Our team of piston pump specialists is here to help if you are looking for high-pressure electric commercial pumps that operate well for your industry. Let’s have a conversation about your needs and obstacles so we can find a solution. Contact Express Drainage Solutions today!