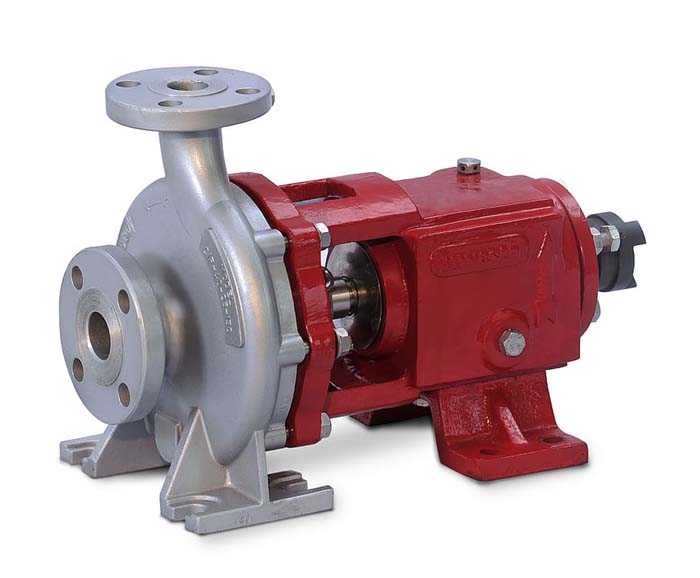
When we talk about a chemical dosing pump, we refer to a pump that helps to introduce chemicals and other substances precisely into a water or gas system. Therefore, in order to prevent waste, the pump regulates the rate at which particles, chemicals, and other solutions are discharged.
The chemical is inserted into tanks or pipes that hold the fluid that is being treated. This occurs after a specific volume of liquid enters the chamber by these dosing pumps. A controller guides the pumps (controls flow rate) and turns the power on and off. Electric motors or an aeration actuation element primarily power the pumps.
How does a chemical dosing pump work?
A dosing pump can work in a number of ways, each tailored to a specific brand and model. Injecting a precisely measured quantity of a chemical into a pipe or other comparable device is key to all of these procedures. In order to set up a chemical dosing pump, you’ll need:
The chemical container or tank
The product being closed,
The foot valve.
A suction pipe connects this one-way valve. It keeps the pump primed and goes into the product drum. There should be some weight on it to keep it from falling to the product drum’s bottom part, and occasionally, a float switch triggers an alarm on the pumps if the product runs out.
The pump itself
The materials and sizes vary, although they are typically made of stainless steel, rubber, or chemically resistant plastics like PE or PVC. One end of the device is connected to the inlet via a suction line, while the other is the dosing line.
The dosage line
This is a reinforced hose, a PE or PVC tube, or something similarly rigid.
Stainless steel is occasionally used for the line in extremely high-pressure, hot water, or steam applications. Typically, it’s merely a line, but it can incorporate various air-release valves, pressure relief, and bleed.
The injector
A product has an injector point where the product is injected into it. The dosing pump may force a certain amount of product into the line. This one-way valve allows it to pass through the delivery pipe despite the pressure. The one-way valve prevents the delivery line liquid from flowing up the dosing line. This is because it can damage the pump once the chemical dosing pump stops or the product shot is released.
Additionally, the injector features a spout that directs the product flow into the center of the flow channel instead of the side walls. The release of some products, particularly oxidizers and acids such as peroxide or chlorine, near the stream’s edge can erode pipe walls over time. To further guarantee an appropriate reaction, releasing the product into the stream’s center generates a vortex, facilitating the product’s mixing.
Control system
The chemical dosing pump is sometimes controlled to activate and deactivate at specific intervals to provide precise dosing. One example is a central control system with chlorine, pH, similar sensors, and variable rate control to raise or lower the dosage level. Others range from a simple timer to a flow switch. A more complicated system for operations may also incorporate it.
What is a Dosing Pump?
A dosing pump can withstand harsh environments, such as extremely high pressures and temperatures. Starting with a set amount of water in its reservoir, a dosing pump will gradually add more water to a pipe or tank until the water is at the dosage level.
3 major types of chemical pumps used
- Diaphragm pumps
This is a positive displacement pump that makes use of a reciprocating diaphragm to transfer liquids-gas and liquid mixtures. There’s a need for more maintenance for these pumps in comparison to others. Additionally, the risk of fluid contamination and oil vapor leakage is eliminated. This is because they do not have any lubrication, seal, or internal wear components.
- Positive displacement pumps
A variety of rotary pumps are available, including piston pumps, screws, gear, and rotary vane. When it comes to pumping fluids with high pressure and viscosity, positive displacement pumps outperform centrifugal pumps. Also, these positive displacement models can handle fluids with low vapor pressure. These are more difficult to pump since they move slower, producing greater resistance.
- Centrifugal pumps
Typically the most cost-effective option, centrifugal pumps are the most prevalent kind of pump. The pumps create a vacuum by sucking liquid into an impeller. Not preparing it properly could result in low suction power, one drawback of this pump.
Chemical gear pumps
Low-viscosity fluids, such as food, industrial chemicals, polymers, pharmaceuticals, hot melt adhesives, prepolymers, and many more, have specific process requirements that they should meet.
These accurate transfer gear pumps are an economical way to increase pressure and stabilize output. They can also handle viscosities ranging from 100 to 250,000 cPs and differential pressures up to 1000 psi. Closely controlled tolerances ensure precise and consistent volumetric production. PSI’s revolutionary, patent-pending lip seal is ideal for adhesive and melt-blown applications. It also performs leak-free in a wide variety of pressures and viscosities, even when placed under vacuum.
Type of pump used for chemical injection
There are two main types of chemical injection pumps: those that run on electricity and those that run on gas. The diaphragm and the piston are the two primary kinds of gas-driven pumps. Pneumatic CIPs are another name for these pumps. Though they use different mechanisms to propel the molecules, they are functionally equivalent.
Chemical injection pumps might be any of several kinds. There are two main types of chemical injection pumps: those that run on electricity and those that run on gas.
Injection pumps that run on gas or pneumatic power
- The diaphragm chemical pump and the single-head, gas-powered positive displacement pump are two examples. The stroke length is proportional to the gas injection volume.
- Metering pumps are versatile enough to handle both water and chemical injections. Their ability to operate at high pressures makes them ideal for averaging continuous flow rates. Diaphragm pumps are the most effective metering tools for preventing leaks. Because they are precise and leak-proof, diaphragm pumps are superior. This makes them more efficient and extends their useful life.
Electric Chemical Injection Pumps:
Although they differ in motor and power, electrical chemical injection pumps are piston-driven and have a common design element. By keeping the system’s gas vents sealed, piston-driven injection pumps aid in operations. Current electric chemical injection pumps are ideal where electricity is unavailable, such as in rural regions. From a financial and ecological standpoint, they are an excellent substitute for pneumatic chemical injection pumps.
Plunger pumps for chemical injection
A packed plunger pump applies pressure to the plungers to inject a predetermined chemical into a process. The amount of chemical injected is determined by multiplying the volume per stroke by the number of strokes per minute. Each stroke injects the required amount of chemicals.
The flow rate of a dosing pump
You can better plan the system’s design if you have a rough notion of the target flow rate. A poor investment in the long term would be installing a chemical dosing pump that is either too big or too small for the job if the necessary flow rate needs to be accurately calculated.
Before you can order the correct pumps, you must determine the following three things:
- The amount of fluid that must be moved during a given time frame
- The amount of space the fluid must fill
- Is the fluid you’re pumping clear or thick? Do you know how hot the fluid being pushed is? Etc.
Your industrial requirements will determine these three factors. The amount of fluid you wish to transfer dictates the pump’s flow rate. The maximum allowable flow rate is quite sensitive to the fluid type and the distance traveled. Thus, the necessary pump type and size depend highly on all three parameters.
Conclusion
Many different types of businesses rely on dosing pumps. Accurate fluid supply is essential for process control and product quality assurance, making it possible. Contact us immediately if you have any questions regarding our chemical dosing pump range or would like to talk about your project with one of our technical experts.