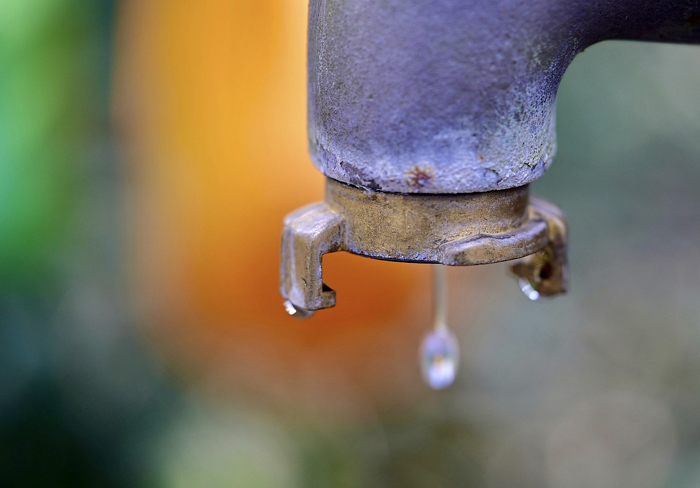
The cleaning agents, their expert application, and the cleaning equipment’s design and operation are the three pillars upon which the success of cleaning membrane systems rests. You can clean membrane systems with chemicals with both high and low pH to yield the greatest results. During normal operation of these systems, the performance of the membrane systems usually decreases. This is because of the buildup of precipitated salts, colloids, small particles, or microorganisms on the surface of the membrane.
A disastrous membrane collapse can occur in a relatively short time due to some of these deposits. Chemical pretreatment and cartridge filtration are examples of pretreatment procedures. They aim to decrease the buildup of these problematic deposits. Fouling, or scaling, describes the accumulation of these particles. In the form of hard crystalline precipitates (scalants), minerals like calcium carbonate and sulfates of calcium, strontium, and barium come together. A few of these deposits have the potential to bring about a catastrophic membrane collapse in a relatively short amount of time.
On the surface of membrane elements are soft deposits called foulants that are made up of silica, biological growth, suspended and colloidal particles, and metal oxides. In order to choose the appropriate cleaning solutions, it is necessary to determine the types of deposits that have settled into the membrane element.
Here’s how to clean membrane systems
Forward flush
When using a forward flush, feed water goes to the membranes in a forward manner. The rate of water flow or permeate through the system is higher during the feed water or permeate flow phase compared to the production phase. The turbulence and quicker flow induce the release and discharge of particles absorbed by the membrane.
3: Using air or water flushes or air flushes
This cutting-edge cleaning technique is known as an air flush or a water/air flush. Injecting air into the supply line is a type of forward flush. The use of air causes the formation of air bubbles, which in turn increases turbulence. This turbulence renders membrane surfaces fouling-free.
Backward Flush
This is a method of filtration that operates oppositely. The permeate is forced out of the system via the feed water side while it is under pressure. By using a backward flush, the membrane pores are flushed from the inside out. Because the pressure outside the membranes is higher than the pressure inside, cleaning of the pores occurs.
4: Using chemicals to clean membranes
- Verify that the cartridge filters, hoses, and cleaning tank are in good working condition. If needed, clean the tank and the hoses. Set up the replacement cartridge filters.
- Fill the cleaning tank with permeate. Start the tank’s recirculation process by activating the agitator or pump.
- Gradually add a cleaning product of your choice to the cleaning tank while stirring thoroughly. The amount needed will depend on the product mix and the entire volume of the Clean-in-Place.
- Verify the solution’s temperature. To achieve the desired temperature, you need to modify the heating control if the solution’s temperature drops below the specified level.
- Make sure the solution’s pH is approximately 12. If the membrane’s pH is too low, you can adjust it with sodium hydroxide or a comparable chemical according to the manufacturer’s instructions. If the pH is excessively high, you can lower it by adding hydrochloric acid.
- In the feed flow direction, cycle the solution through each stage for 30 minutes. Make sure to circulate the fluid at the recommended rate for the system or membrane. During cleaning, it is important to maintain a low enough pressure to ensure minimal permeation.
- In very foul situations, it is best to direct the first return flow to the drain. This is to prevent the redeposition of removed materials. For optimal performance in a multistage system, it is necessary to clean each stage separately.
- In the event that the first-stage cleaning solution turns stained or muddy, empty the tank and make a fresh one. It is necessary to prepare a fresh solution in the event that its temperature or pH falls outside of the specified range. Regardless, it would be best if you made a fresh cleaning solution for every step.
- Rinse the system thoroughly with reverse osmosis permeate before re-instating it.
- Wait for the product water to drain completely to ensure that all cleaning solutions are out of the system before turning it back on.
Best chemical for cleaning a membrane system
Using a chemical to clean a membrane system helps remove impurities from the membrane filter. This is done by using the reactions between chemical reagents, deposits, and other pollutants that impact flux rates. These chemical substances are there all the way, from bases and acids to formulated and oxidizing agents. Metal sulfide, iron oxide, and calcium carbonate are only some of the deposits that the acid can dissolve. The hydroxides, carbonates, and phosphates in the cleaning solution are alkaline. They may disperse, emulsify, and loosen the deposits with ease. Using a combination of acid and alkaline agents is the best strategy for eliminating stubborn deposits, including silicates.
Alkaline Cleaning:
It is useful for removing some inorganic deposits, grease, and organic fouling. Examples of common alkaline solutions include potassium hydroxide and sodium hydroxide. The process involves adjusting the pH of the alkaline solution as it is pumped through the membrane system in order to improve cleaning efficiency. To remove any remaining alkalinity, it is essential to rinse thoroughly.
- Acid Cleaning:
The product helps to eliminate inorganic fouling, metal oxides, and mineral scale deposits. Phosphoric acid, citric acid, and hydrochloric acid are common acids. Step one involves circulating the acid solution through the membrane system for a certain amount of time. Step two involves washing the membrane system thoroughly.
Why do you need to clean the membrane?
Cleaning and maintaining membrane systems on a regular basis is essential to ensuring their optimal performance. A system can become contaminated if you don’t clean it regularly. There’s a hindrance to energy consumption and performance recovery. It happens if this problem is not checked or rectified over an extended period of time.
How do you backwash membranes?
This is a filtration process that happens in reverse. With twice the flux applied during filtering, permeate is pushed under pressure through the system’s feed water side. It is possible to use a chemical cleaning procedure if the flux has not recovered enough during back flushing.
The membrane’s pores are turned inside out when using the backward flush technique. Cleaning happens in the holes because the pressure on the membrane’s permeate side is greater than the pressure within the membranes. The pressure used to accomplish a backward flush is approximately 2.5 times higher than the pressure used for production.
In order to ensure that the permeate chamber remains contamination-free, permeate is consistently utilized for backward flushes. Process recovery is reduced as a result of reverse flushing. This means that the time required for a backward flush ought to be as minimal as possible. But you have to keep the flush going long enough to flush a module’s volume once.
Is it right to use hydrogen peroxide to clean the membrane?
Biological and organic pollutants are the most common types of fouling in ultrafiltration membranes that are used to clean water and wastewater. Oxidative chemicals like hydrogen peroxide are often used to clean membrane systems because they are so good at getting rid of these pollutants.
Which membrane needs frequent cleaning to prevent clogging?
Reducing fouling and improving membrane performance are two main reasons why cleaning membrane systems is essential. Consequently, membrane separation operations in water treatment are in dire need of an efficient cleaning approach right now. A thorough investigation into cleaning methods is necessary to remove fouling and generally enhance membrane effectiveness.
To prevent membrane fouling and other problems, pretreatment is usually necessary for RO and NF membranes. This is because their pores are smaller compared to MF and UF membranes.
Conclusion
Making sure the valve in the distribution system is completely closed while cleaning is important. This is to prevent chemicals from unintentionally getting into the drinking water system. Depending on its capacity, the somewhat polluted water can be directed to the waste effluent system.